I help influencers get their merch made in Vietnam
My name is Chris Walker. I am a Vietnam sourcing expert with 15+ years experience in Ho Chi Minh City. I serve influencers and start-ups that want to work directly with factories. I am not an agent. If you want to produce in Vietnam, then I can help you.
Let's meet on Zoom.
Let's meet on Zoom.
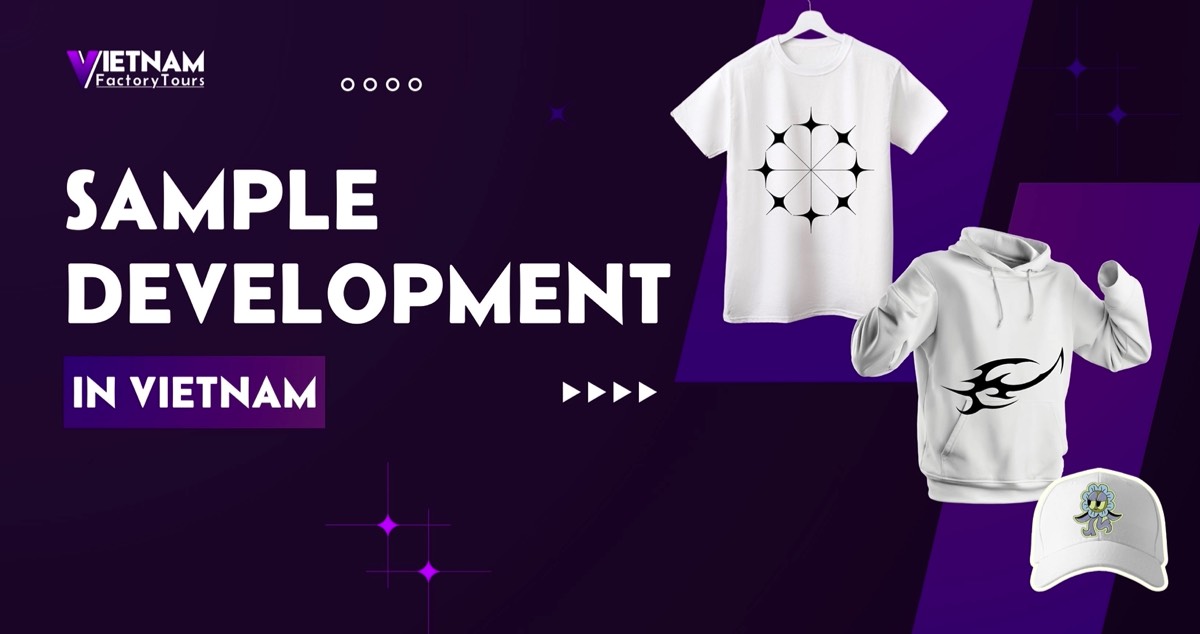
My History in Vietnam
I came here in 2008 and fell in love with the energy of the people. I felt safe and the food was amazing. I started working as a marketing manager for a t-shirt factory which is how I learned the business of producing merch for influencers.
Fast forward to today and I offer the following services: webinars, courses, consulting, tours and sample development.
Where are you in your business journey? Why is Vietnam on your mind?
Fast forward to today and I offer the following services: webinars, courses, consulting, tours and sample development.
Where are you in your business journey? Why is Vietnam on your mind?
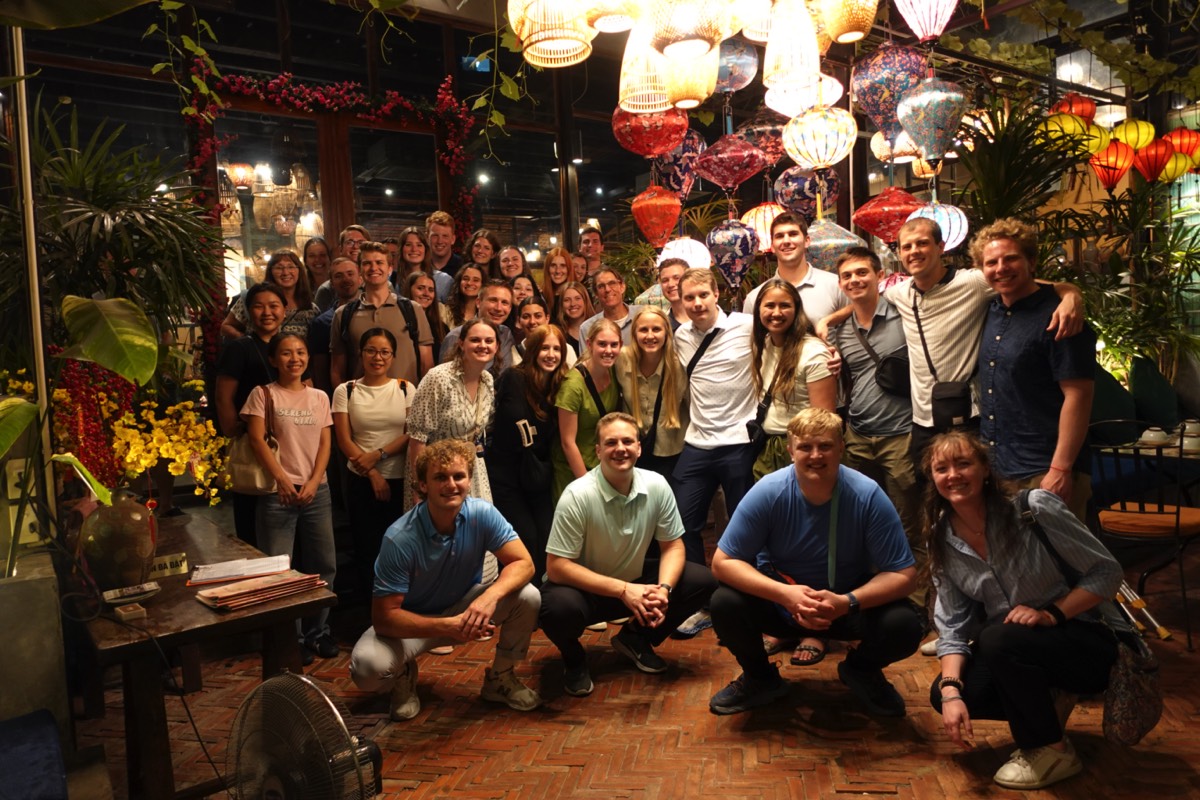
The first step to making apparel merch is choosing your fabric.
Fabric is the most important part of a garment and the factory will ask you many questions about your fabric. If you are not familiar with textile engineering then here are some tips.
Be prepared to answer the following:
Are your garments made from woven or knit fabrics?
What is the fiber composition?
What is the color of the fabric?
What is the weight of the fabric?
Be prepared to answer the following:
Are your garments made from woven or knit fabrics?
What is the fiber composition?
What is the color of the fabric?
What is the weight of the fabric?
Are your garments made from woven or knit fabrics?
Sewing factories either produce garments made with woven fabric or garments made with knit fabric. Make sure you know the difference between woven and knit so that you make a good impression on the factory.
The best example of a woven fabric is a men’s dress shirt. The best example of a knit fabric is a t-shirt. Woven fabric does not stretch. Knit fabric stretches. There are hundreds of fabric variations that will make your head spin; at a minimum you MUST be clear about this simple distinction: Woven vs Knit. If a factory asks you, “is your fabric woven or knit” and you answer with, “I am not sure” then they will know that you are a beginner.
Woven fabric is made on a loom and does not stretch (unless it has spandex.) Examples of garments made with woven fabric are: toga dress, blazer, wedding dress, dress shirt, jeans, and surf trunks.
Knit fabric is made on a circular knit machine or flat knit machine. Examples of knitted fabrics are: T-shirt, polo shirt, hoodie, sweater, beanie hat, and socks.
Boxers can be made with either woven or knit fabric.
Cardigans can be made with either woven or knit fabric.
Pencil dresses can be made with either woven or knit fabric.
Pajamas can be made with either woven or knit fabric.
A fabric has a “structure”. There are two sub-groups of knit structures: weft vs. warp. Woven fabric has many structure variations. Here are some examples:
• Single Jersey
• Interlock
• Pique
• Rib
• Ponte Roma
• Jacquard
Some examples of warp knitted structures are:
• Tricot
• Milanese
• Rachel
Some examples of woven fabric structures are
• Twill Denim
• Rib Weave
• Chiffon
• Oxford
• Basket Weave
a. Natural Fibers
i. Cotton, Viscose, Bamboo, Linen, Silk, Wool, Hemp
b. Synthetic Fibers
i. Polyester, Acrylic, Nylon, Acetate, Spandex and Kevlar
Once you choose your fibers/yarns then specify the percentages like 95%/5%.
When it comes to discussing the fabric, you have two options. You can tell the Vietnam factory the exact fabric composition or give them a physical sample of fabric to copy.
The best example of a woven fabric is a men’s dress shirt. The best example of a knit fabric is a t-shirt. Woven fabric does not stretch. Knit fabric stretches. There are hundreds of fabric variations that will make your head spin; at a minimum you MUST be clear about this simple distinction: Woven vs Knit. If a factory asks you, “is your fabric woven or knit” and you answer with, “I am not sure” then they will know that you are a beginner.
Woven fabric is made on a loom and does not stretch (unless it has spandex.) Examples of garments made with woven fabric are: toga dress, blazer, wedding dress, dress shirt, jeans, and surf trunks.
Knit fabric is made on a circular knit machine or flat knit machine. Examples of knitted fabrics are: T-shirt, polo shirt, hoodie, sweater, beanie hat, and socks.
Boxers can be made with either woven or knit fabric.
Cardigans can be made with either woven or knit fabric.
Pencil dresses can be made with either woven or knit fabric.
Pajamas can be made with either woven or knit fabric.
A fabric has a “structure”. There are two sub-groups of knit structures: weft vs. warp. Woven fabric has many structure variations. Here are some examples:
Weft knit clothing fabric stretches in one direction.
Some examples of weft knit structures are:• Single Jersey
• Interlock
• Pique
• Rib
• Ponte Roma
• Jacquard
Warp knit fabrics stretch in two directions
A classic example of a warp knit fabric is bathing suit fabric.Some examples of warp knitted structures are:
• Tricot
• Milanese
• Rachel
Some examples of woven fabric structures are
• Twill Denim
• Rib Weave
• Chiffon
• Oxford
• Basket Weave
Do you know the fiber composition of your fabric?
Now that you know the knitting or weaving structure of your fabric, the next step is to inform the factory what the fiber composition is. Yarn and fiber are synonymous in this context. Here are the options.a. Natural Fibers
i. Cotton, Viscose, Bamboo, Linen, Silk, Wool, Hemp
b. Synthetic Fibers
i. Polyester, Acrylic, Nylon, Acetate, Spandex and Kevlar
Once you choose your fibers/yarns then specify the percentages like 95%/5%.
When it comes to discussing the fabric, you have two options. You can tell the Vietnam factory the exact fabric composition or give them a physical sample of fabric to copy.
What is the color of the fabric?
Factories expect to hear a Pantone number when you speak about color. The Pantone color scheme is an industry standard way to indicate exact colors. Fashion designers, merchandisers, and dye-houses use Pantone colors to be on the same page. A good factory will have a light box where you can compare two pieces of fabric to the Pantone color card. Be sure to study up on the Pantone color system before you approach the factory.
What is the weight of the fabric?
The weight of the fabric is measured in g/m2 or oz/yd2. It is important to understand how fabric weight is measured so you can test it yourself. A circle test is the industry standard and there are special circular scissors and special scales designed specifically for this purpose. The first time you see them in real life you will “get it.” Here is a picture of scale and a circular cutter. If the factory does not have these scissors or scales then be careful.
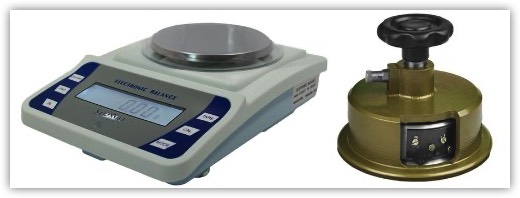
T-shirt-fabric-weight ranges from 100 g/m2 to 280 g/m2. 100 g/m2 would be a light weight t-shirt. 280 g/m2 would be a heavy fleece. Denim fabric typically weighs 270 g/m2. Weighing relaxed-fabric versus not relaxed fabric can give different results. Moisture content in the fabric can affect the weight. Usually clients need to give the desired weight within a tolerance of +- 5%. Weight is important because it will effect the price and the “feel” of the garment.
In Conclusion: These are basic fabric topics that will arise during your discussions with a factory in Vietnam. The more informed you are, the easier it will be to work quickly with the factory. Getting the fabric right is half the battle.
In Conclusion: These are basic fabric topics that will arise during your discussions with a factory in Vietnam. The more informed you are, the easier it will be to work quickly with the factory. Getting the fabric right is half the battle.
Here is one factory in our network that you can visit.
American Fashion factory based in Ho Chi Minh City produces its own brand of underwear and can produce underwear for you too. Join one of our Vietnam Factory tours and see how underwear is made in Vietnam.
Let's Start Working Together in Vietnam
Download a Free Starter Kit
I have collected resources that will help you prepare to meet factories:
- eBook: Make Tech Packs in Vietnam
- Sample Tech Pack
- Quantity Breakdown List
- Sample Quality Control Check List
- Import Duty Calculation Guide
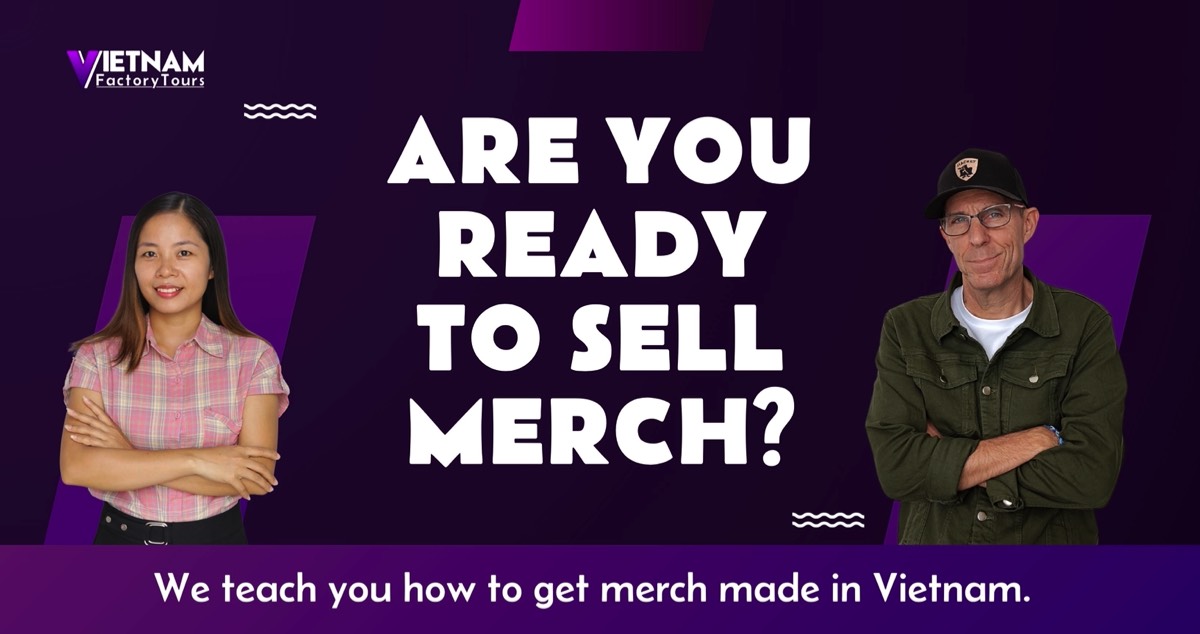
Join My Weekly Webinar
Each Friday I host a webinar at 10 pm Vietnam time. Each person introduces themself and then I give a 20 minute presentation on 7 Rookie Mistakes to Avoid when producing in Vietnam. Then each person gets to ask at least one question which I answer as best I can based on my 15+ years experience working in Vietnam. Sign up here.
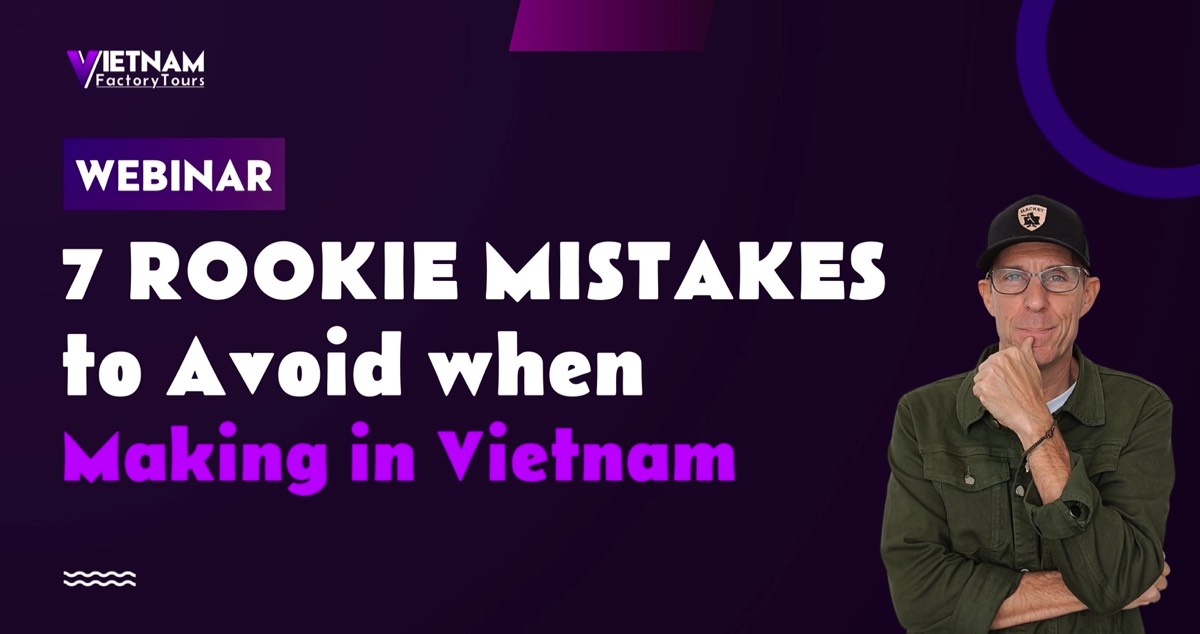
Complete My Online Courses
I share 15 years of lessons learned in an online course that consists of 21 videos approximately 10 min each. Learn what factories care about, how to calculate your target price, how to create tech packs, how visit factories, how to negotiate price, how to arrange for shipping, calculate your tax, negotiate contracts…and more. Start course here.
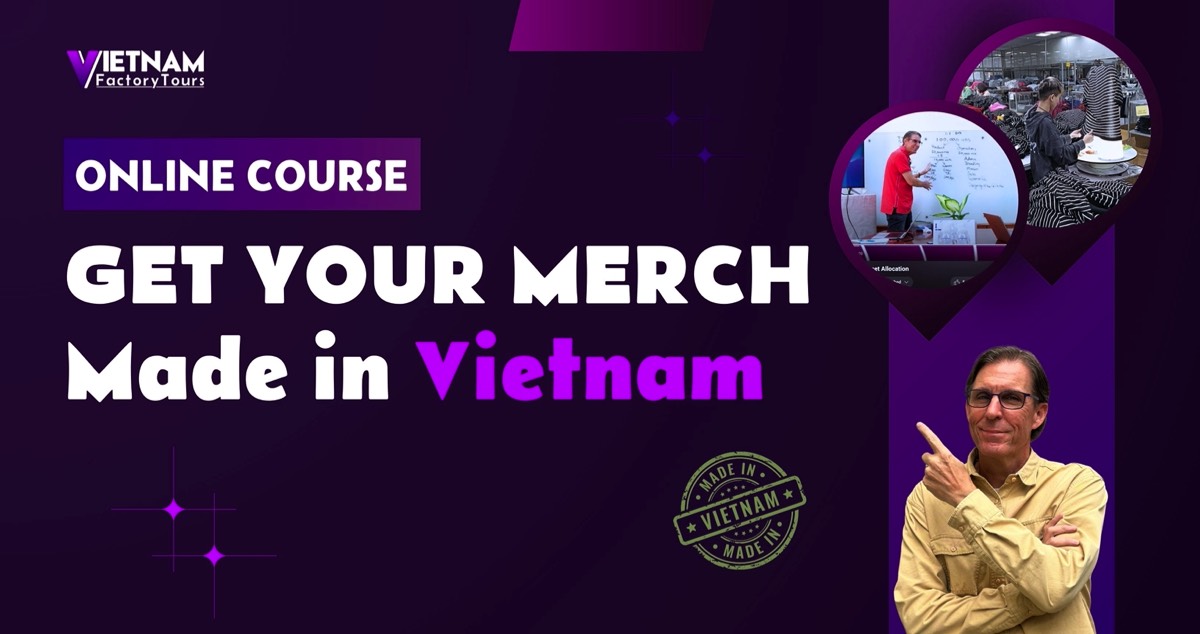
Go on Factory Tours
Hire us to take you to visit 3-5 factories in a day. We pick you up at 7:30 am and get you to the first factory at 8 am. Price includes car, driver, translator and lunch. You will be the star of the show. Book a tour today!
Or learn more at our website: www.vietnam-factory-tours.com
Or learn more at our website: www.vietnam-factory-tours.com
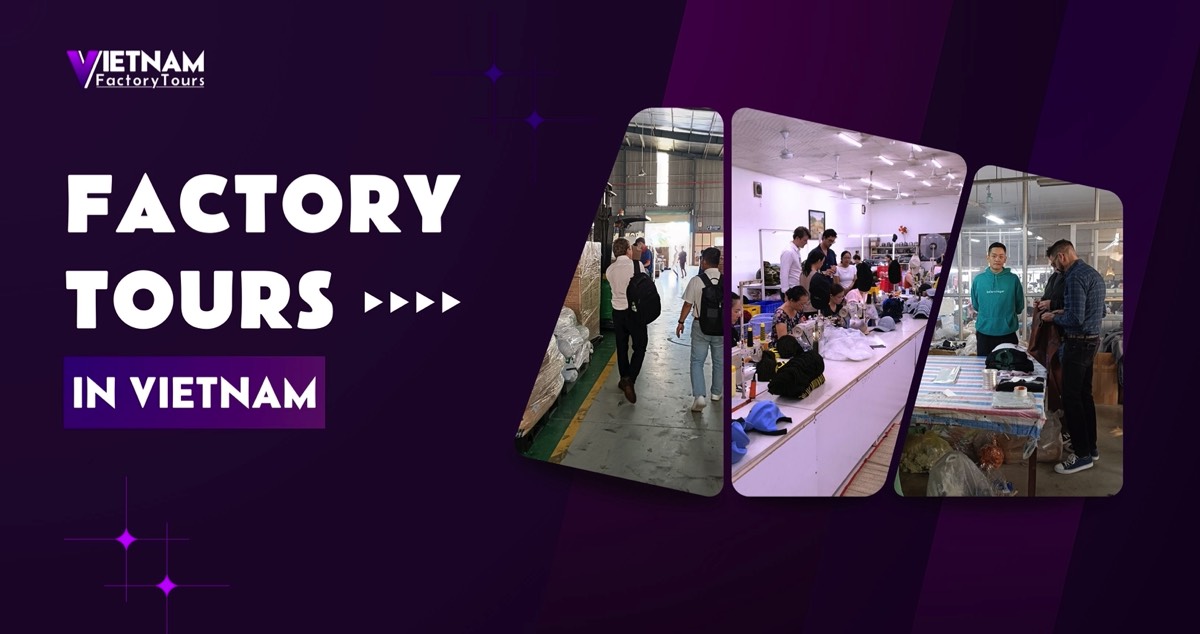